Composite Diamond Coating®
Composite Diamond Coating® is a unique, patented coating with ultra-fine diamond particles contained within hard electroless nickel metal with numerous benefits including:
- Exceptional wear resistance
- Excellent hardness
- Enhanced corrosion resistance
- Perfect conformity to complex geometries including non-line-sight applications
- Increased thermal transfer
- Applicability to all common metals and alloys
- Coverage of entire surfaces or selected critical areas
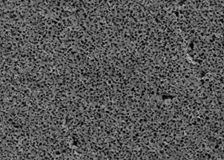
|
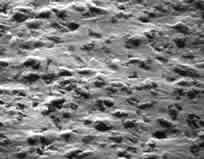
|
1000x Cross Section of
Composite Diamond Coating®
|
Photograph of the surface of
Composite Diamond Coating®
|
By applying diamond coatings to your metal parts you can increase lifetime and minimize maintenance related downtime due to the replacement of high wear parts. In addition, any process parts enhanced by a wear resistant coating like Composite Diamond Coating® will produce more consistent product over an extended period of time. Most metal finishers agree that the presence of this unique coating may also allow new materials with other performance or cost advantages to be utilized.
Composite Diamond Coating® has long been a standard and economical solution to the extreme wear conditions in the high-speed textile industry. Composite Diamond Coating® has also proven to be advantageous in the following industries:
- Gear
- Paper
- Molding
- Tool and die
- Plastics
- Packaging
- Petrochemical
- Automotive
Composite Diamond Coating® has received a positive review from the U.S. Food and Drug Administration (FDA) Department of Health and Human Services. Click here for details.
The following are a number of questions typically asked by prospective plating services of Composite Diamond Coating®, as well as brief answers to these questions.
What is the appearance?
Composite Diamond Coating® is a unique and attractive matte gray color. When used or polished the coating becomes shinier and more metallic in appearance. The Nano-Plate™ version of Composite Diamond Coating® is inherently a shinier nickel colored coating. These coatings can be subsequently coated with other materials if an alternate final appearance is desired.
How perfect is the uniformity?
Because of the electroless chemical method of deposition, Composite Diamond Coating® covers all surfaces of the work piece with essentially perfect uniformity. There is no build up on edges, corners, inner diameters, or any other surface. Another significant advantage of Composite Diamond Coating® over other coating processes such as electroplating, spray, and other types of coatings is that Composite Diamond Coating® can be applied with uniformity to all surfaces of parts regardless of geometry. Recesses, holes, inner diameters of any size; there is no “line of sight” requirement for Composite Diamond Coating®.
What thicknesses are possible?
The thickness of Composite Diamond Coating® can be customized according to the requirements of each specific application. Any thickness from 0.0002” (5 microns) to over 0.025” (625 microns) can be produced with Composite Diamond Coating®, although most applications use a standard coating thickness of 0.001” (25 microns). Any thickness can be applied to a tolerance of about +/- 2 microns.
How high is the diamond density?
The density of diamond particles within Composite Diamond Coating® is typically 40% by volume. Higher and lower densities can be produced as needed, but the standard range serves well in virtually all applications. Too little diamond in the coating will not sufficiently provide the properties of diamond desired in the coating. Too much diamond in the coating would mean not enough of the metal matrix required for adhesion to the part and structural integrity of the coating itself.
What diamond particle sizes can be used?
The standard and most commercially used versions of Composite Diamond Coating® are CDC-2 and CDC-8, which incorporate diamond particles with a mean particle size of 2 or 8 microns, respectively. Other sizes may also be used. Particles of up to about 40 microns in size may be used when required for high friction and grip. On the smaller side, Surface Technology, Inc. has developed its Nano-Plate™ version of Composite Diamond Coating®™ which features diamond particles in the nanometer size range. Incorporating such nanometer sized diamond means a tremendous increase in diamond surface area within the composite, yet with few automorphic or cleavage faces thanks to the generally rounded surfaces of these advanced particles. The resulting composite is compatible with a wide array of mating materials including textiles, paper, plastics, seals, metals, and alloys. In some cases, Nano-Plate™ actually exhibits lubricating properties along with outstanding wear resistance.
How good is the diamond quality?
The diamond incorporated into Composite Diamond Coating® is very precisely specified for composition, size, and shape. As the large surface area of the diamond particles interact with the reactive electroless nickel bath, the purity of the diamond must be exceptional. In order to insure both the optimal density of diamond within the coating and the surface characteristics of the coating, the diamond must be tightly sized and shaped.
What is the surface finish?
Surface Technology, Inc. uses only finely graded diamond within rigid sizing specifications for Composite Diamond Coating®. This produces a very uniform coating without variations in roughness. Surface Technology, Inc. does however offer other coatings that provide a rougher texture when needed for high friction and grip.
In certain especially delicate applications where even greater smoothness is required, there are three main options to consider:
- The standard Composite Diamond Coating® can be lightly sandblasted, polished, or tumbled before use.
- An electroless nickel overcoat may also be applied to provide a break-in layer for parts upon initial use.
- The Nano-Plate™ version of Composite Diamond Coating® that employs smaller diamond particles can be applied.
How hard is CDC?
Composite Diamond Coating® is made up of two materials: electroless nickel and diamond. The hardness of heat-treated electroless nickel is about 950 Vickers, while diamond is an extraordinary 10,000 Vickers. Combined, the hardness of Composite Diamond Coating® averages about 1,200 - 1,500 Vickers. While significantly high in comparison to other materials such as tool steel (400 Vickers) and chrome plating (1,000 Vickers), it is complicated to establish absolute hardness readings on composite materials such as Composite Diamond Coating®; and it is in its tremendous wear resistance and other properties that Composite Diamond Coating®™ really shines.
What is the wear resistance?
Various standardized test methods have been employed to evaluate wear resistance of different materials and coatings. Perhaps the most common test method is the Taber abrasive wear test. In the Taber test method, a coated panel turns under two rotating abrasive wheels, usually CS-10 type. Wear is measured as the weight loss of the panels following a specified number of rotating cycles under a fixed load. The lower the wear index, the lower the wear to the coating. The coatings and materials in the following table were tested by 1,000 cycles on the Taber test device.
Coating or Material |
Wear Index
|
Composite Diamond Coating®
Cemented Tungsten Carbide
Grace C-9 (88WC, 12 Co)
Electroplated Hard Chromium
Tool Steel, Hardened Rc 62
|
0.0115
0.0274
0.0469
0.1281
|
Following are Taber abrasion test results for Nano-Plate™ and hard chrome plating. These results are based on a more extensive test of 10,000 cycles.
Coating |
Wear Index
|
Nano-Plate™
Hard chrome plating
|
0.0013
0.04
|
Many other test methods have been used to demonstrate the exceptional wear resistance of Composite Diamond Coating® over other coatings and materials. For example, in the Yarnline Abrasive Wear Test where an abrasive Yarnline under constant tension is drawn across a material sample at a constant speed and force against the test piece. Results are measured in material removal over time as mil3 per hour. The following are results from this testing:
Coating or Material |
Wear Rate
|
Composite Diamond Coating®
Cemented Tungsten Carbide
Flame Sprayed Aluminum Oxide
Electroplated Hard Chrome
Hardened Tool Steel
|
1.3
43.7
173.6
966.6
3478.6
|
In an abrasive slurry test program, steel panels with and without coating were wear tested by an Alumina slurry of 5 micron powder contacting the panel surface under a constant load. The wear data was converted to a new constant, equating the volume of material lost (microns3) per unit force (Newton) for unit length (mm). The following results show the advantage of Composite Diamond Coating®™ over conventional electroless nickel and bare steel.
Coating |
Wear
Constant
|
Wear
vs. Steel
|
Wear
vs. EN
|
None
Electroless Nickel
Composite Diamond Coating®
|
28
16
7
|
—
0.57
0.25
|
1.75
—
0.44
|
What does it cost?
The cost of Composite Diamond Coating®™ is surprisingly economical for a number of key reasons.
- Surface Technology, Inc. has a customized, state of the art production facility to produce this and its other coatings on a daily basis.
- Surface Technology, Inc. uses only plating components it manufactures on site for the Composite Diamond Coating®™ process, thereby making the product at a further reduced cost and ensuring optimal quality.
- The cost of Composite Diamond Coating®™ is relatively low when consideration is given to its outstanding wear life, and the savings that can be realized from extending use and reliability.
- Given the unique properties of Composite Diamond Coating®™, many customers are able to change the base material of their parts to one that is less expensive, lighter, or easier to manufacture, thereby creating an additional cost saving.
- As Composite Diamond Coating®™ can be chemically removed by Surface Technology, Inc., used parts can be returned to have the old coating removed and recoated to yield a part that is as good as new without the cost of manufacturing another part.
In general, the price to coat parts with Composite Diamond Coating®™ is determined based on the size of the parts (both overall size and the area to be coated), amount of masking or fixturing required, coating thickness, base material, and quantity of parts.
What substrates can be coated?
Essentially any metal or alloy can be enhanced by Composite Diamond Coating®. The most common materials coated are carbon or tool steels and aluminum alloys. Copper, brass, bronze, stainless steel, and titanium are also regularly treated with Composite Diamond Coating®™. It should be noted, however, that the extended pretreatment process required for stainless steel and titanium make the coating onto these materials more expensive than common steels or aluminum. Fortunately, the exceptional wear and corrosion resistance properties of Composite Diamond Coating®™ allows the substitution of these more expensive materials such as titanium and carbide with less expensive alternatives like aluminum and steel.
Is selective coating or masking possible?
Selective deposition of Composite Diamond Coating®™ is certainly achievable when required. It is important to know for each part which critical areas must be treated, which areas may not be treated for specific reasons, and which areas may or may not be treated depending on the greatest economy and expediency of the coating process. Often it is less expensive and faster to coat "non-critical" areas than to mask off these areas.
What post-treatment may be done?
After coating, a heat treatment step is generally desirable to provide improved adhesion of the coating, greater hardness of the matrix, and maximum wear resistance. A heat treatment of up to 750°F is normally preferred. Other temperatures can be implemented as needed for specific applications or to maintain necessary substrate material specifications.
What are the environmental benefits?
Composite Diamond Coating® offers a number of important environmental benefits in comparison to alternative coating technologies:
- Composite Diamond Coating® uses no chrome. The environmental problems inherent with plating and using chrome are therefore entirely eliminated.
- Composite Diamond Coating® can be routinely produced with up to 40% by volume of codeposited particles. This means that at least 40% less nickel is required to produce composite coatings of equal thickness compared with conventional coatings without such particles.
- Given the greater wear resistance of Composite Diamond Coating® versus conventional coatings, the deposit thickness of Composite Diamond Coating® can be significantly less than conventional electroless or electroplated nickel coatings. This means even less nickel needs to be used.
- Composite Diamond Coating® lasts longer, and parts will need to be recoated or replaced less frequently; again, resulting in even less nickel used.
- The less nickel the plating shop uses, the longer their baths will last. This means less baths required, less waste treatment, and less waste.
- Greater wear resistance of Composite Diamond Coating® reduces the release of the coating into the environment.
Because Composite Diamond Coating® can be chemically stripped, used parts can be stripped and recoated, thereby reclaiming the nickel metal in solution form for recycling.
Is CDC Patented?
Covered by one or more of the following United States Patents No. 4,997,686, 5,145,517, 5,300,330, 5,863,616, 6,306,466, 7,744,685, 8,147,601, 8,598,260, 9,096,924 and 10,006,126, with others pending.