Products & Services
Creator of Composite Diamond Coating®
Surface Technology, Inc. is the creator and technical leader of CDC - Composite Diamond Coating®, an exceptionally engineered coating of electroless nickel with fine diamond. The synergy of these materials makes CDC an exceptionally hard and wear resistant coating. CDC conforms to even the most complex geometries and is an excellent replacement for chrome plating. STI makes CDC available via coating services from its production facility as well as chemical products sold directly, through a network of distributors, and by agreement with licensees worldwide.
Contact STI for One-Plate® Electroless Nickel solutions, the simplest EN in the world. These One-Plate® systems use just one “Q” solution for both bath make-up and replenishment. This innovation by STI overcomes the many shortcomings of using three A, B, and C solutions. Available in low, medium, high phosphorous, and composite EN varieties. Naturally, all are RoHS compliant.”
Flame Retarding Coatings
Surface Technology, Inc. recognizes that flame retardation is an important area of concern in the world. As is well presented in the United Nations Environment Programme, International Programme on Chemical Safety, Environmental Health Criteria 192, Flame Retardants: A General Introduction; the toll to human life and property is substantial. As this document points out.
“In today’s society, there is an unprecedented development in the size and number of buildings, skyscrapers, warehouses and methods of transport. Carpeting, furnishings, equipment, oil and gas for heating all increase the fire load in a building.” “Modern fire-fighting techniques, equipment and building design have reduced the destruction due to fires. However, a high fuel load in either a residential or commercial building can offset even the best of building construction.” “Each year, over 3 million fires leading to 29,000 injuries and 4,500 deaths are reported in the USA. The direct property losses exceed $8 billion and the total annual cost has been estimated at over $100 billion.”
Since ancient times a large number of methods have been developed to retard fires including material selection, chemical treatments, and protective coatings. Despite these efforts, certain requirements of fire protection have not been met due to the limitation of the methods developed to date. For this reason, STI has invested its expertise and research and development capabilities toward a new method of providing such protection.
The collapse of the World Trade Center buildings on September 11, 2001 provided a devastating example. A May 2002 report on the tragedy by the Federal Emergency Management Agency and the American Society of Civil Engineers concluded that, “The fact that the structures were able to sustain this level of damage and remain standing for an extended period of time is remarkable and is the reason that most building occupants were able to evacuate safely.” However, as the report also notes, “the twin towers could have withstood the impact of the two hijacked Boeing 767 airliners that plowed into the trade center…The towers succumbed to the ensuing fire … that softened the buildings’ steel framework.” One of the report’s investigators said, “The impact of the jets is believed to have blown off the fluffy fireproofing material on the trade center’s steel columns, making them susceptible to the intense heat from the ensuing fire.” A conclusion of the federal report was that, “Fireproofing that sticks to steel beams and emergency stairwells ‘hardened’ to withstand catastrophic impact of a plane should be included in high-risk buildings.”
The “fluffy” fireproofing as used in the World Trade Centers is a common defense against fire. Another common method is to incorporate particles of flame retarding materials into painted layers used in building construction. An inherent deficiency of these two methods lie in their method of application to the structures they are intended to protect. Such materials to date are sprayed or painted onto structures. The bond between the fire retardants and the base material is therefore not optimal.
STI’s development in this field relates to the composite plating onto materials for fireproofing purposes. Various plating methods are available where a metallurgical bond between the coating and the metal substrate is achieved. Further, STI has made it possible to incorporate fine insoluble particles of fire retarding materials into the plated layer, thereby creating an integral composite. The composite layer can feature a metallurgical bond to the base metal and fireproofing properties. The improved adhesion of such coatings compared to spray applied materials is substantial and leads to greater integrity of the structure to withstand both impact and fire.
An additional advantage of this new STI development is the opportunity to apply a composite plated layer as portrayed above plus the additional step of applying a secondary overcoat layer comprised of the same or other flame retardant material as utilized within the initial composite layer. Because of the protrusion of the flame retardant particulate material on the surface of the composite plated layer (which would appear in general as in the photograph below), the adhesion or bonding of the overcoat layer to the like material in the composite layer will be promoted. This could be used for polymerizing additional materials to the composite plated coating.
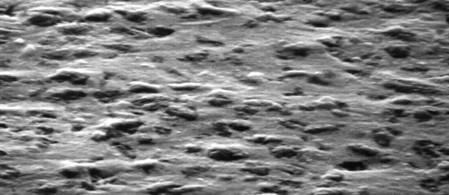
Photograph of surface of a composite plated layer with protruding particles
This development by STI has potential benefits for a larger variety of structures including buildings, vehicles, security devices, and other materials and objects.